Chevrolet Trax: Wheel drive shaft outer joint inspection
Disassembly Procedure
- Remove the outer constant velocity (CV) joint and boot from the wheel
drive shaft. Refer to Front Wheel
Drive Shaft Outer Joint and Boot Replacement.
- Remove any lubricant from the CV joint.
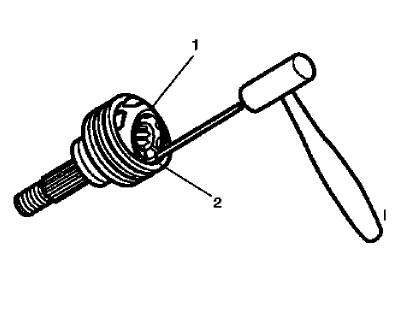
Fig. 64: Taping Gently On Brass Drift With A Hammer In Order To Tilt Cage
NOTE: Position the cage and the inner race so they are level.
- Install the outer CV joint assembly in a soft jawed vise.
NOTE: The following procedure will have to be repeated until all
the ball bearing
are removed from the cage.
- Using a brass drift (1), gentle tap the cage (2) until the ball bearing
can be removed from the cage (2).
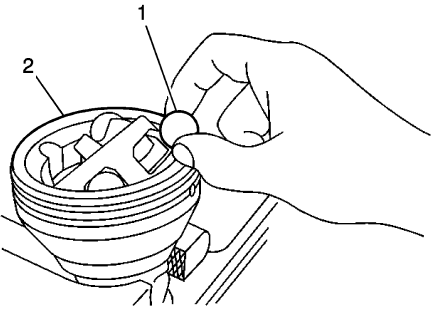
Fig. 65: Removing/Install Ball From Cage & Inner Race
- Using a small screwdriver, remove the ball bearings (1) from the CV
joint (2).

Fig. 66: View Of Ball Removal/Installation Sequence
- Remove the ball bearings from the CV joint in sequence.
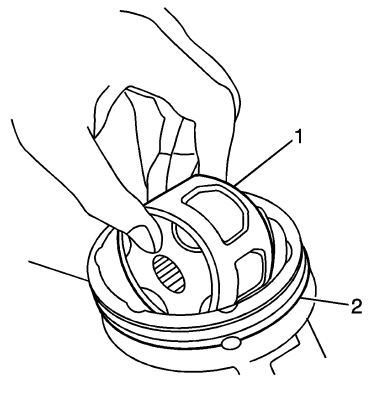
Fig. 67: Positioning Cage & Inner Race 90 Degrees To Centerline Of Outer Race
NOTE: Position the cage so that the larger radius corners of the
cage windows
are facing up.
- Position the cage (1) at a 90 degrees to the centerline of the outer
race (2).
- Align the cage windows with the lands of the outer race (2).
- Lift and remove the cage (1) and the inner race from the outer race (2).
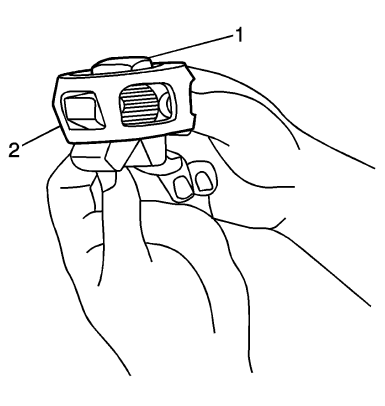
Fig. 68: Positioning Cage So Larger Radius Corners Of Cage Windows Are Up
- Position the cage (2) and the inner race (1) so that the larger radius
corners of the cage windows are up.
- Rotate the inner race (1) 90 degrees to the center line of the cage (2).
- Align the lands of the inner race (1) with the windows of the cage (2).
- Move the inner race (1) land into the cage window (2).
- Rotate the inner race (1) down and remove it from the cage (2).
- Clean the following items thoroughly with the proper cleaning solvent:
- The inner race
- The outer race
- The cage
- The ball bearings
- The exposed end of the wheel drive shaft
NOTE: The internal parts of the CV joint are NOT SERVICED
separately. The outer
CV joint is serviced as an assembly.
- If any of the above items are found to have excessive wear or are
damaged, replace the outer CV joint as
an assembly.
Assembly Procedure
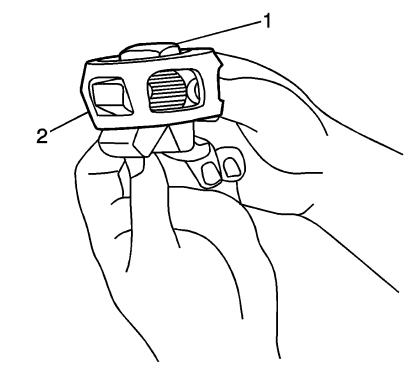
Fig. 69: Positioning Cage So Larger Radius Corners Of Cage Windows Are Up
- Position the cage (2) so that the larger radius corners of the cage
windows are up.
- Position the inner race (1) 90 degrees to the centerline of the cage
(2).
- Insert the inner race (1) through the bottom of the cage (2).
- Align the lands of the inner race (1) with the windows of the cage (2).
- Move the inner race (1) land into the cage window (2).
- Rotate the inner race (1) down and remove it from the cage (2).
- Rotate the inner race (1) within the cage (2) so that the grooved
surface of the inner race (1) is facing up.
- Align the inner race (1) ball bearing tracks with the cage (2) windows.
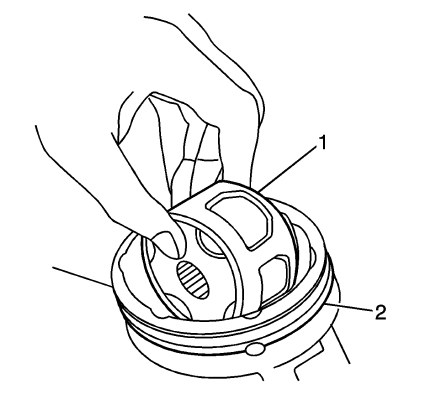
Fig. 70: Positioning Cage & Inner Race 90 Degrees To Centerline Of Outer Race
- Wrap a clean shop towel around the CV joint outer race spined shaft.
- Place the outer race (2) vertically in a bench vise.
- Position the cage (1) and the inner race at a 90 degrees to the
centerline of the outer race (2).
- With the inner race and the cage (1) assembly in a vertical position,
insert the cage and the inner race into
the outer race (2).
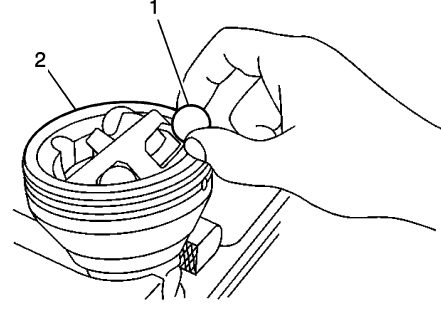
Fig. 71: Removing/Install Ball From Cage & Inner Race
NOTE: The larger radius corners of the cage windows should be
positioned up
and the grooved surface of the inner race should be visible.
- Position the cage (2) and the inner race so that they are level in the
vise.
- Rotate the appropriate component(s), and align the cage windows and the
inner race ball bearing (1)
tracks with the outer race ball bearing tracks.
- Position a cage window and the inner race ball bearing track for the
ball bearing installation.
NOTE: When performing the following procedure, the opposing cage
(2) window
and the inner ball bearing (1) track will be accessible for the ball bearing
installation.
- Press down on the cage following one of the outer race ball bearing (1)
tracks.
- Install the ball bearing through the cage window onto the inner race
ball bearing (1) track.
NOTE: The following service procedure will have to be performed
after each ball
bearing (1) has been installed.
- After the first ball bearing (1) has been installed, use a brass drift
and a hammer and gently tap the cage in
order to drive the cage and the inner race down completely in the outer race.
NOTE: After the ball bearing (1) has been installed, there should
be NO GAP
between the ball bearing and the inner race.
- Position the cage and the inner race so that they are level.
- Using a plastic hammer, lightly tap the ball bearing (1) into place.
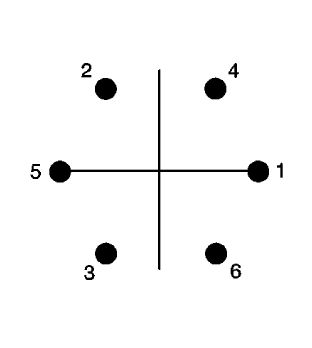
Fig. 72: View Of Ball Removal/Installation Sequence
- Install the ball bearings in sequence.
- Repeat steps 18 thru 20 until all the ball bearings are installed.
- Install the outer CV joint and boot on the wheel drive shaft. Refer to
Front Wheel Drive Shaft Outer
Joint and Boot Replacement.
Wheel drive shaft inner joint inspection
Inspection Procedure
- Remove the front wheel drive shaft inner joint and boot. Refer to Front
Wheel Drive Shaft Inner Joint
and Boot Replacement.
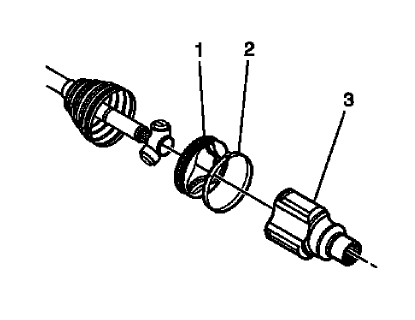
Fig. 73: Identifying Wheel Drive Shaft Inner Joint Inspection Areas
- Remove the wheel drive shaft tripod bushing (1) from the tripod housing
(3).
- Remove the wheel drive shaft tripod housing (3) from the wheel drive
shaft.
- Remove the wheel drive shaft tripod joint boot bushing (1).
- Using a suitable cleaner, remove the excess grease from the tripod
assembly.
- Inspect the following items for damage or excessive wear:
- The wheel drive shaft tripod boot
- The wheel drive shaft tripod assembly
- The wheel drive shaft tripod joint housing
- The wheel drive shaft tripod joint bushing
- The wheel drive shaft
READ NEXT:
WHEEL DRIVE SHAFTS DESCRIPTION AND OPERATION
Front wheel drive axles are flexible assemblies.
Front wheel drive axles consist of the following components:
A front wheel drive shaft tripot joint (in
WHEEL ALIGNMENT SPECIFICATIONS
ENCLAVE
ENCLAVE w/o QPR
ENCLAVE w/QPR
ENCORE
ENCORE All Models
LACROSSE
LaCROSSE GNA Base Suspension
LaCROSSE GNB Performance Suspension
REGAL
REGAL GNA Ba
SEE MORE:
Fig. 33: Front Fog Lamp
Front Fog Lamp Replacement (Trax)
FRONT FOG LAMP REPLACEMENT (ENCORE)
Fig. 34: Front Fog Lamp
Front Fog Lamp Replacement (Encore)
FRONT FOG LAMP BULB REPLACEMENT (TRAX)
Fig. 35: Front Fog Lamp Bulb
Front Fog Lamp Bulb Replacement (Trax)
FRONT FOG LAMP BULB R
Special Tools
CH-50559 Wheel Hub/Bearing Remover Kit
For equivalent regional tools, refer to Special Tools.
Removal Procedure
Raise and support the vehicle. Refer to Lifting and Jacking the Vehicle
.
Remove the steering knuckle. Refer to Steering Knuckle Replacement.
Fig. 10: Steering Knuckl