Chevrolet Trax: Crankshaft and bearing installation
Special Tools
- EN-235-6 Installer from EN-235-D Kit.
- EN-470-B Angular Torque Wrench
- EN-658-1 Installer from EN-658 Kit
For equivalent regional tools, refer to Special Tools.
- Lubricate crankshaft, crankshaft bearings and crankshaft bearing cap tie
plate with engine oil.
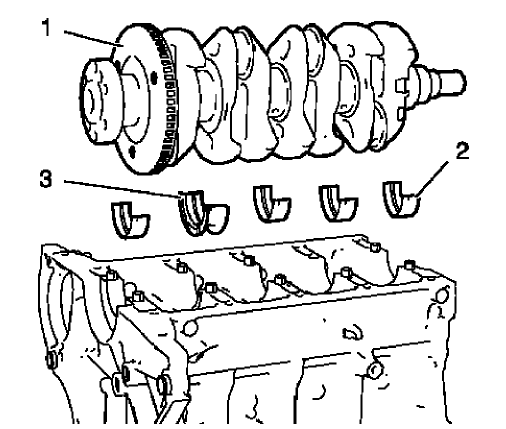
Fig. 385: Crankshaft, Upper Crankshaft Bearings And Upper Crankshaft Thrust
Bearing
- Install the 4 upper crankshaft bearings (2) and the crankshaft thrust
bearing (3).
- Install the crankshaft (1).
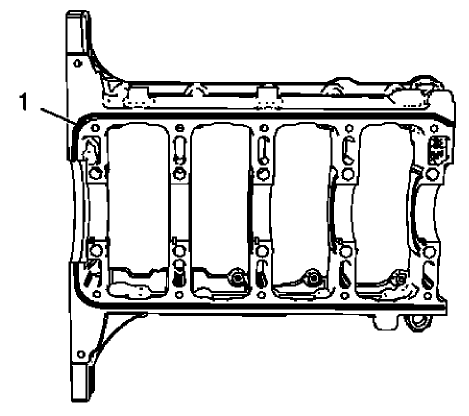
Fig. 386: Sealing Compound Application Area
NOTE: The thickness of the sealing bead should be 2 mm
(0.0787 in).
- Apply sealing compound (1) to the outer rim of the groove on the
crankshaft bearing cap tie plate. Refer
to Adhesives, Fluids, Lubricants, and Sealers.
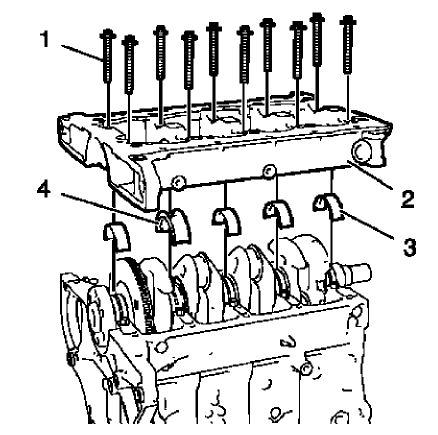
Fig. 387: Crankshaft Bearing Cap Tie Plate
NOTE: The complete installation procedure should not take longer
than 10
minutes.
- Install the 4 lower crankshaft bearings (3) and the lower crankshaft
thrust bearing (4).
- Install the crankshaft bearing cap tie plate (2).
NOTE: Do not reuse the old bolts.
- Install the 10 NEW inner crankshaft bearing cap tie plate bolts (1).
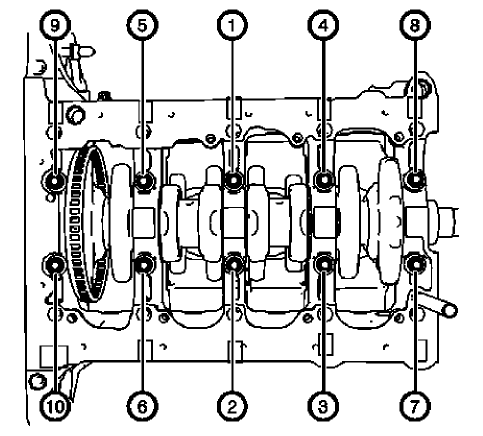
Fig. 388: Inner Crankshaft Bearing Cap Tie Plate Bolts Tightening Sequence
CAUTION: Refer to Fastener Caution .
CAUTION: Refer to Torque-to-Yield Fastener Caution .
- Tighten the 10 inner crankshaft bearing cap tie plate bolts in the
sequence shown and to the following
specifications:
- Tighten the inner crankshaft bearing cap tie plate bolts to 25 N.m (18
lb ft).
- Tighten the inner crankshaft bearing cap tie plate bolts an additional
60 degrees. Use EN-470-B
wrench.
- Tighten the inner crankshaft bearing cap tie plate bolts an additional
15 degrees. Use EN-470-B
wrench.
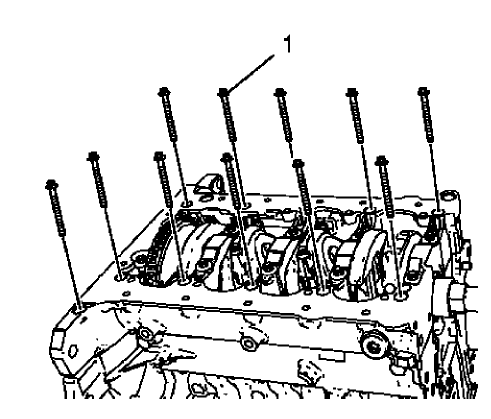
Fig. 389: Outer Crankshaft Bearing Cap Tie Plate Bolts
NOTE: Do not reuse the old bolts.
- Install the 12 NEW outer crankshaft bearing cap tie plate bolts (1) and
tighten to the following
specification:
- Tighten the outer crankshaft bearing cap tie plate bolts to 10 N.m (89
lb in).
- Tighten the outer crankshaft bearing cap tie plate bolts an additional
60 degrees. Use EN-470-B
wrench.
- Tighten the outer crankshaft bearing cap tie plate bolts an additional
15 degrees. Use EN-470-B
wrench.

Fig. 390: Crankshaft Position Sensor, Bolt And Seal Ring
- Install the crankshaft position sensor (1) and a NEW crankshaft position
sensor seal ring (2).
- Install the crankshaft position sensor bolt (3) and tighten to 8 N.m (71
lb in).
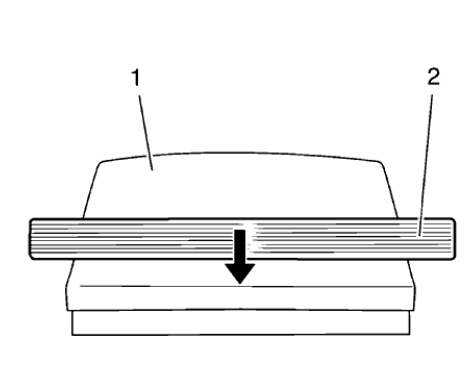
Fig. 391: Crankshaft Rear Oil Seal
- Slide the crankshaft rear oil seal (2) across the EN-235-6 installer (1)
contained in EN-235-D kit.
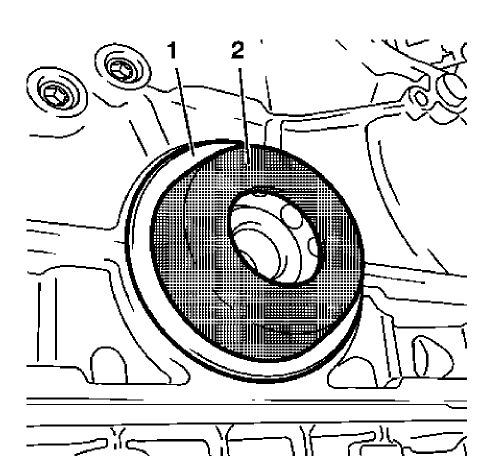
Fig. 392: Crankshaft Rear Oil Seal And Installer
- Install the crankshaft rear oil seal (1) with EN-235-6 installer (2) to
the crankshaft.

Fig. 393: Oil Seal Installer
NOTE: Ensure that the crankshaft rear oil seal fits proper.
- Use EN-658-1 installer (2) to strike the crankshaft rear oil seal (1)
PISTON, CONNECTING ROD, AND BEARING INSTALLATION
Special Tools
EN-470-B Angular Torque Wrench
For equivalent regional tools, refer to Special Tools.
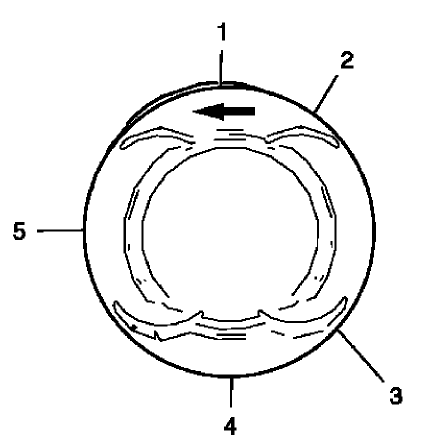
Fig. 394: Piston Ring Joint Adjustment Points
- Adjust the piston ring joints as follows:
- Upper compression ring (1).
- Lower compression ring (4).
- Oil rings (2) or (3).
- Oil ring spacer (5)
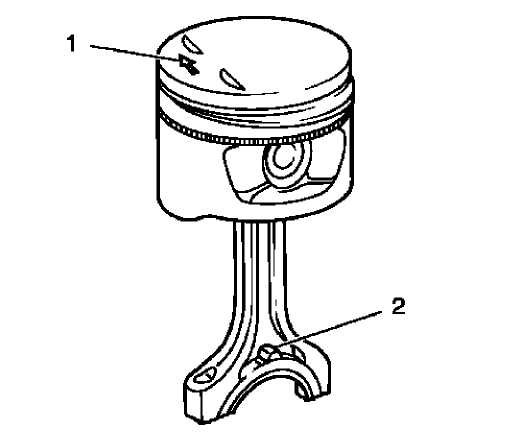
Fig. 395: Rods And Arrow On Piston Head
- The arrow (1) on the piston head must point to the timing side.
- The markings on the connecting rods (2) must point to the transmission
side.
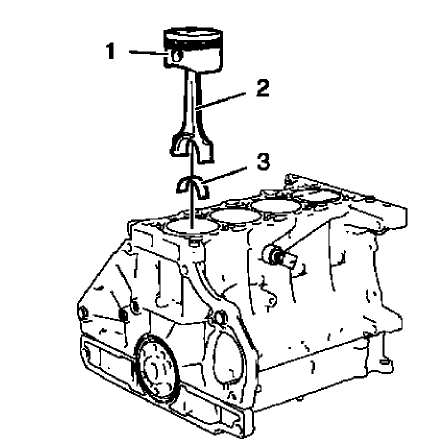
Fig. 396: Pistons, Connecting Rods And Bearings
- Install a piston ring compressor to compress the piston rings.
- Install the pistons (1) in along with connecting rods (2) and upper
connecting rod bearings (3) to the
engine block and to the crankshaft.
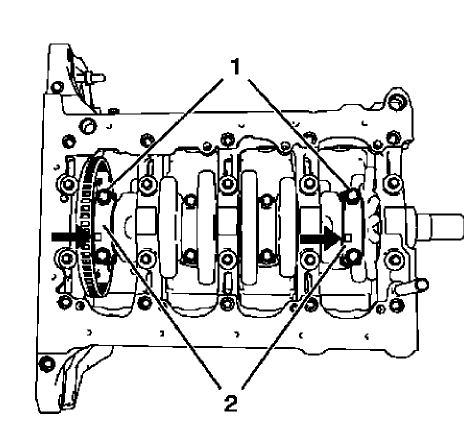
Fig. 397: Rod Bearing Caps And Bolts
NOTE: The flarings (arrows) on the connecting rod bearing caps must
point to the
transmission side. The connecting rod bearing caps must be installed in
their original position.
- Install the 2 connecting rod bearings and the 2 connecting rod bearing
caps (2) of cylinder 1 and 4.
CAUTION: Refer to Fastener Caution
CAUTION: Refer to Torque-to-Yield Fastener Caution .
NOTE: Do not reuse the old bolts.
- Install the 4 NEW connecting rod bearing cap bolts (1) and tighten in
the following sequence:
- Tighten the connecting rod bearing cap bolts to 25 N.m (18 lb ft).
- Tighten the connecting rod bearing cap bolts an additional 45 degrees.
Use EN-470 B wrench
- Rotate the crankshaft 180 degrees.
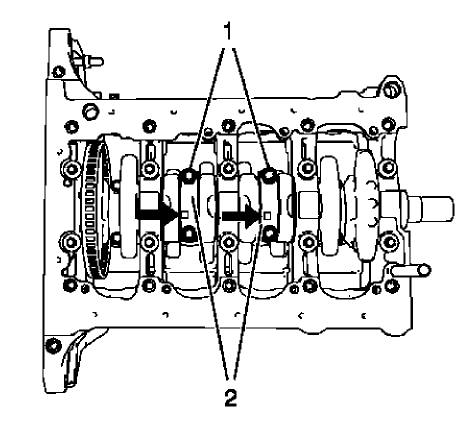
Fig. 398: Rod Bearing Caps And Bolts
NOTE: The flarings (arrows) on the connecting rod bearing caps must
point to the
transmission side. The connecting rod bearing caps must be installed in
their original position.
- Install the 2 connecting rod bearings and the 2 connecting rod bearing
caps (2) of cylinder 3 and 2.
NOTE: Do not reuse the old bolts.
- Install the 4 NEW connecting rod bearing cap bolts (1) and tighten in
the following sequence:
- Tighten the connecting rod bearing cap bolts to 25 N.m (18 lb ft).
- Tighten the connecting rod bearing cap bolts an additional 45 degrees.
Use EN-470-B wrench.
READ NEXT:
Special Tools
EN-470-B Angular Torque Wrench.
For equivalent regional tools, refer to Special Tools.
WARNING: Wear safety glasses when using compressed air in order to
prevent
eye injury.
Clean th
Special Tools
EN-952 Fixing Pin
EN-953-A Fixing Tool
EN-955-10 Fixing Pin from EN-955 Kit
For equivalent regional tools, refer to Special Tools.
The engine should be adjusted to TDC.
The crank
Special Tools
EN-49980 Guidance Pins
For equivalent regional tools, refer to Special Tools.
Clean the sealing surfaces from old sealing material, dirt, oil and
grease.
Fig. 421: Engine Front Co
SEE MORE:
A computer system called OBD II
(On-Board Diagnostics-Second
Generation) monitors the operation
of the vehicle to ensure emissions
are at acceptable levels, helping to
maintain a clean environment. The
malfunction indicator lamp comes
on when the vehicle is placed in
ON/RUN, as a check to show it is
The battery is not rechargeable. To
replace the battery:
Caution
When replacing the battery, do
not touch any of the circuitry on
the transmitter. Static from your
body could damage the
transmitter.
Extend the key blade and open
the battery cover on the back of
the transmitter by prying with a