Chevrolet Trax: Brake rotor/drum balance inspection
- Support the vehicle drive axle on a suitable hoist. Refer to Lifting and
Jacking the Vehicle .
- Remove the tire and wheel assemblies from the drive axle. Refer to Tire
and Wheel Removal and
Installation .
- Reinstall the wheel nuts in order to retain the brake rotors.
- Run the vehicle at the concern speed while inspecting for the presence
of the vibration.
CAUTION: Do not depress the brake pedal with the brake rotors and/or
the
brake drums removed, or with the brake calipers repositioned away
from the brake rotors, or damage to the brake system may result.
- If the vibration is still present, remove the rotors from the drive
axle, then run the vehicle back to the
concern speed.
- If the vibration is eliminated when the brake rotors are removed from
the drive axle, repeat the test with
one rotor installed at a time. Replace the rotor that is causing or
contributing to the vibration concern.
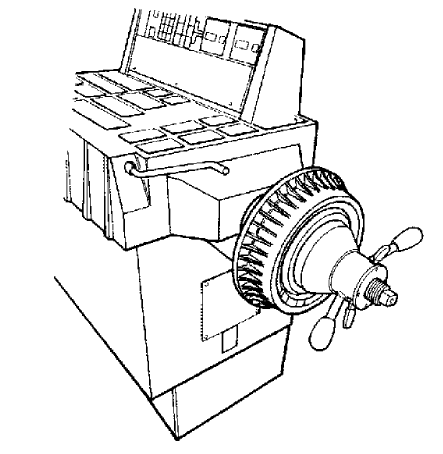
Fig. 12: Balancing Brake Drum
- If a brake rotor was replaced as a result of following the previous
steps, or if necessary to confirm the
results obtained during the previous steps, and/or to check the non-drive
axle components, perform the
following:
- Mount the brake rotor/drum on a balancer in the same manner as a tire
and wheel assembly.
NOTE: Check brake rotors/drums for static imbalance only; ignore
the
dynamic imbalance readings.
- Inspect the rotor/drum for static imbalance.
There is not a set tolerance for brake rotor/drum static imbalance. However,
any brake rotor/drum measured in
this same manner which is over 21 g ( 3/4 oz) may have the potential to cause or
contribute to a vibration.
Rotors/drums suspected of causing or contributing to a vibration should be
replaced. Any rotor/drum that is
replaced should be checked for imbalance in the same manner.
HUB/AXLE FLANGE AND WHEEL STUD RUNOUT INSPECTION
Special Tools
GE-8001 Dial Indicator Set
For equivalent regional tools, refer to Special Tools and Equipment.
- Raise and support the vehicle. Refer to Lifting and Jacking the Vehicle
.
- Mark the location of the wheels to the wheel studs and mark the specific
vehicle position on each tire and
wheel - LF, LR, RF, RR.
- Remove the tire and wheel assemblies from the vehicle. Refer to Tire and
Wheel Removal and
Installation .
- Remove the brake rotors and/or brake drums from the vehicle. Clean the
mounting surfaces of the brake
rotors, the brake drums, if equipped, and the hub/axle flanges of any loose
debris, rust, and corrosion.
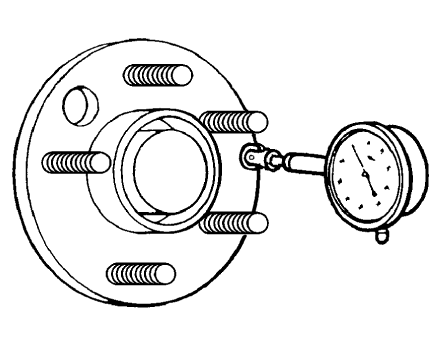
Fig. 13: Measuring Wheel Hub/Axle Flange Runout
- Position the GE-8001 Dial Indicator Set , or equivalent, on the machined
surface of the wheel hub/axle
flange outside of the wheel studs.
- Rotate the hub one complete revolution in order to find the low spot.
- Set the GE-8001 Dial Indicator Set , or equivalent, to zero at the low
spot.
- Rotate the hub one more complete revolution and measure the total amount
of wheel hub/axle flange
runout.
Specification
Wheel hub/axle flange runout tolerance guideline: 0.132 mm (0.005 in)
- If the runout of the wheel hub/axle flange IS within specification and
the vehicle is equipped with wheel
studs, proceed to step 13.
- If the runout of the wheel hub/axle flange IS within specification and
the vehicle is equipped with wheel
bolts, proceed to step 19.
- If the runout of the wheel hub/axle flange is marginal, the wheel hub
may or may not be the source of the
disturbance.
- If the runout of the wheel hub/axle flange is excessive, replace the
wheel hub/axle flange. Measure the
runout of the new wheel hub/axle flange.
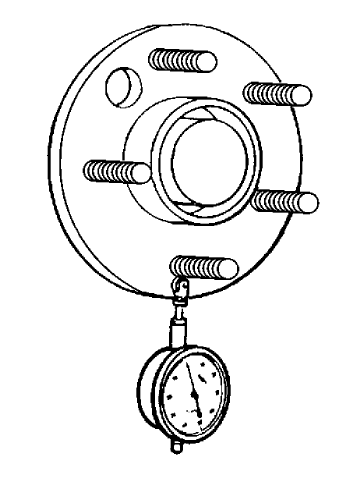
Fig. 14: Measuring Wheel Stud Runout
- Position the GE-8001 Dial Indicator Set , or equivalent, in order to
contact the wheel mounting studs.
Measure the stud runout as close to the flange as possible.
- Turn the hub one complete revolution to register on each of the wheel
studs.
- Zero the GE-8001 Dial Indicator Set , or equivalent, on the lowest stud.
- Rotate the hub one more complete revolution and measure the total amount
of wheel stud - stud circle -
runout.
Specification
Wheel stud runout tolerance guideline: 0.254 mm (0.010 in)
- If the runout of the wheel studs - stud circle - is marginal, the wheel
studs may or may not be contributing to the disturbance.
- If the runout of the wheel studs - stud circle - is excessive, replace
the wheel studs as necessary. Measure
the runout of the new wheel studs.
- Inspect the threads and the tapered seat portion on each of the
wheel bolts for damage.
- Wheel bolts exibiting damaged threads and/or damaged tapered seats
require replacement.
- Place the threaded portion of each wheel bolt along a straight edge to
inspect for straightness.
- Wheel bolts that are not straight require replacement.
TIRE AND WHEEL ASSEMBLY ISOLATION TEST
Force Variation
Force variation refers to a radial or lateral movement of the tire and wheel
assembly which acts much like
runout, however, force variation has to do with variations in the construction
of the tire. These variations in tire
construction may actually cause vibration in a vehicle, even though the tire and
wheel assembly runout and
balance may be within specifications.
Radial Force Variation
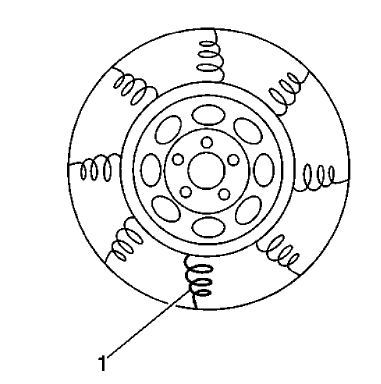
Fig. 15: Identifying Radial Force Variation
Radial force variation refers to the difference in the stiffness of a tire
sidewall as the tire rotates and contacts the
road. Tire sidewalls have some stiffness due to splices in the different plies
of the tire, but these stiffness
differences do not cause a problem unless the force variation is excessive.
Stiff spots (1) in a tire sidewall can
deflect a tire and wheel assembly upward as the assembly contacts the road.
Lateral Force Runout
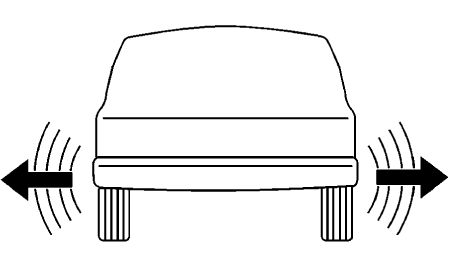
Fig. 16: Identifying Tire Wobble/Waddle
Lateral force variation refers to the difference in the stiffness or
conformity of the belts within a tire as the tire
rotates and contacts the road. Tire belts may have some stiffness or conformity
differences, but these differences
do not cause a problem unless the force variation is excessive. These variations
in the belts of the tire can
deflect the vehicle sideways or laterally. A shifted belt inside a tire may
cause lateral force variation.
In most cases where excessive lateral force variation exists, the vehicle will
display a wobble or waddle at low
speeds, 8-40 km/h (5-25 mph), on a smooth road surface.
Isolation Test Procedure
Perform the following test in order to determine if force variation is
present in the vehicle.
- Substitute a set of KNOWN GOOD, pre-tested tire and wheel assemblies of
the same size and type for
the suspected original assemblies. Refer to Tire and Wheel Removal and
Installation .
- Road test the vehicle to determine if the vibration is still present.
Refer to Vibration Analysis - Road
Testing (EL-38792-A Electronic Vibration Analyzer), Vibration Analysis -
Road Testing (CH-
51450-NVH Oscilloscope).
- If the vibration is still present while using the known good set of tire
and wheel assemblies, then force
variation is not the cause of the vibration.
- If the vibration is eliminated when using the known good set of tire and
wheel assemblies, install one of
the original tire and wheel assemblies using the matchmarks made prior to
removal. Refer to Tire and
Wheel Removal and Installation , . Road test the vehicle to determine if the
vibration has returned.
Refer to Vibration Analysis - Road Testing (EL-38792-A Electronic Vibration
Analyzer), Vibration
Analysis - Road Testing (CH-51450-NVH Oscilloscope).
- Continue the process of installing the original tire and wheel
assemblies one at a time, then road testing
the vehicle, until the tire and wheel assembly, or assemblies which is
causing the vibration has been
identified.
- Replace the tire, or tires on the vibration-causing tire and wheel
assembly, or assemblies, then balance the
assembly, or assemblies. Refer to Tire and Wheel Assembly Runout Measurement
- Off Vehicle.
READ NEXT:
TIRE AND WHEEL ASSEMBLY BALANCING - OFF VEHICLE
WARNING: Failure to adhere to the following precautions before tire
balancing can
result in personal injury or damage to components:
Clean away any d
Vibration Theory
The designs and engineering requirements of vehicles have undergone drastic
changes over the last several
years.
Vehicles are stiffer and provide more isolation from road input than
SEE MORE:
Special Tools
GE-8001 Dial Indicator Set
For equivalent regional tools, refer to Special Tools.
NOTE: This inspection procedure does not supersede local government
required
inspections that have more stringent requirements.
Turn the ignition key to the ON position with the engine OFF.
Fig. 4:
Removal Procedure
WARNING: Refer to Brake Dust Warning .
Raise and support the vehicle. Refer to Lifting and Jacking the Vehicle
.
Remove the front tire and wheel assembly. Refer to Tire and Wheel
Removal and Installation .
Remove the front brake rotor. Refer to Front Brake Rotor Replacement