Chevrolet Trax: Repair instructions
TIRE AND WHEEL ASSEMBLY BALANCING - OFF VEHICLE
WARNING: Failure to adhere to the following precautions before tire
balancing can
result in personal injury or damage to components:
- Clean away any dirt or deposits from the inside of the wheels.
- Remove any stones from the tread.
- Wear eye protection.
- Use coated weights on aluminum wheels.
Tire and Wheel Assembly Balancer Calibration
Tire and wheel balancers can drift out of calibration over time, or can
become inaccurate as a result of heavy
use. There will likely not be any visual evidence that a calibration problem
exists. If a balancer is not calibrated
within specifications, and a tire and wheel assembly is balanced on that
machine, the assembly may actually be
imbalanced.
Tire and wheel assembly balancer calibration should be checked approximately
every 2 weeks, if the machine is
used frequently, and/or whenever the balance readings are questionable.
Tire and Wheel Assembly Balancer Calibration Test
NOTE: If the balancer fails any of the steps in this calibration
test, the balancer should
be calibrated according to the manufacturer's instructions. If the balancer
cannot be calibrated, contact the manufacturer for assistance.
Inspect the calibration of the tire and wheel assembly balancer according to
the manufacturer's
recommendations, or perform the following test.
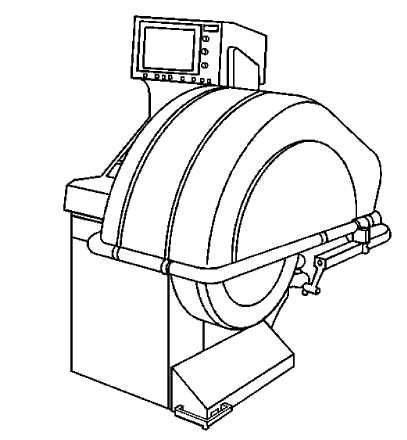
Fig. 17: View Of Tire & Wheel Assembly Balancer
- Spin the balancer without a wheel or any of the adapters on the shaft.
- Inspect the balancer readings.
Specification
0 within 7 g ( 1/4 oz)
- If the balancer is within the specification range, balance a tire and
wheel assembly - that is within radial
and lateral runout tolerances - to ZERO, using the same balancer.
- After the tire and wheel assembly has been balanced, add an 85 g (3 oz)
test weight to the wheel at any
location.
- Spin the tire and wheel assembly again. Note the readings.
- In the static and dynamic modes, the balancer should call for 85 g (3
oz) of weight, 180 degrees
opposite the test weight.
- In the dynamic mode, the weight should be called for on the flange of
the wheel opposite the test
weight.
- With the assembly imbalanced to 85 g (3 oz), cycle the balancer 5 times.
- Inspect the balancer readings:
Specification
Maximum variation-7 g ( 1/4 oz)
- Index the tire and wheel assembly on the balancer shaft, 90 degrees from
the previous location.
- Cycle the balancer with the assembly at the new location.
- Inspect the balancer readings:
Specification
Maximum variation-7 g ( 1/4 oz)
- Repeat steps 8-10 until the tire and wheel assembly has been cycled and
checked at each of the 4
locations on the balancer shaft.
Tire and Wheel Assembly Balancing Guidelines
NOTE: Tire and wheel assemblies which exhibit excessive runout can
produce
vibrations even if the assemblies are balanced.
It is strongly recommended that the tire and wheel assembly runout be
measured and corrected if necessary BEFORE the assemblies are balanced.
If the runout of the tire and wheel assemblies has not yet been measured,
refer to Tire and Wheel Assembly
Runout Measurement - Off Vehicle before proceeding.
There are 2 types of tire and wheel balance:
Static Balance
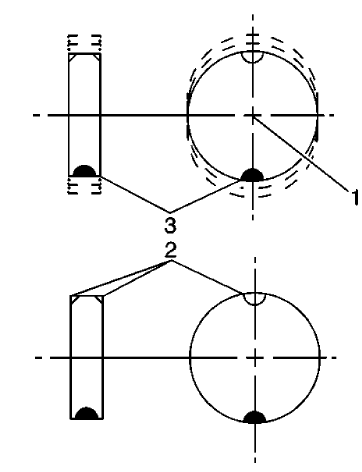
Fig. 18: View Of Static Balance
Static balance is the equal distribution of weight around the wheel
circumference. The wheel balance weights
(2) are positioned on the wheel in order to offset the effects of a heavy spot
(3). Wheels that have static
imbalance can produce a bouncing action called tramp.
Dynamic Balance
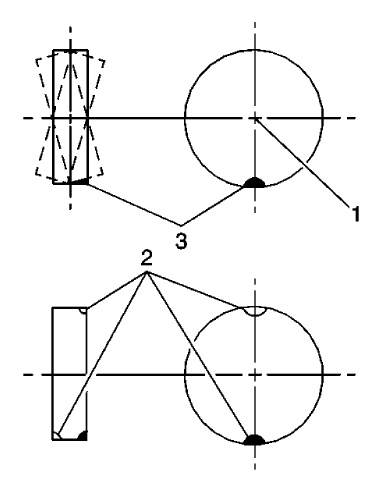
Fig. 19: View Of Dynamic Balance
Dynamic balance is the equal distribution of weight on each side of the tire
and wheel assembly centerline. The
wheel balance weights (2) are positioned on the wheel in order to offset the
effects of a heavy spot (3). Wheels
that have dynamic imbalance have a tendency to move from side to side and can
cause an action called shimmy.
Most off-vehicle balancers are capable of checking both types of balance
simultaneously.
As a general rule, most vehicles are more sensitive to static imbalance than to
dynamic imbalance; however,
vehicles equipped with low profile, wide tread path, high performance tires and
wheels are susceptible to small
amounts of dynamic imbalance. As little as 14-21 g ( 1/2 - 3/4 oz) imbalance is
capable of inducing a vibration
in some vehicle models.
Balancing Procedure
CAUTION: Refer to Vehicle Lifting and Jacking Caution
NOTE: When balancing tire and wheel assemblies, use a known good,
recently
calibrated, off-vehicle, two-plane dynamic balancer set to the finest balance
mode available.
- Raise and support the vehicle.
- Mark the location of the wheels to the wheel studs and mark the specific
vehicle position on each tire and
wheel - LF, LR, RF, RR.
- Remove the tire and wheel assemblies one at a time and mount on a
spin-type wheel balancer. Refer to
Tire and Wheel Removal and Installation .
- Carefully follow the wheel balancer manufacturer instructions for proper
mounting techniques to be used
on different types of wheels.
Regard aftermarket wheels, especially those incorporating universal lug
patterns, as potential sources of
runout and mounting concerns.
- Be sure to use the correct type of wheel balance weights for the type of
wheel rim being balanced. Be
sure to use the correct type of coated wheel balance weights on aluminum
wheels. Refer to Wheel Weight
Usage.
- Balance all four tire and wheel assemblies as close to zero as possible.
- Using the matchmarks made prior to removal, install the tire and wheel
assemblies to the vehicle. Refer to
Tire and Wheel Removal and Installation .
- Lower the vehicle.
Wheel Weight Usage
Tire and wheel assemblies can be balanced using either the static or dynamic
method.
Clip-on Weights
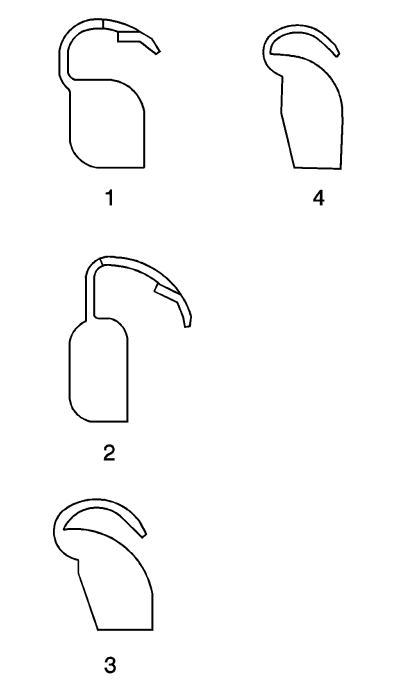
Fig. 20: Identifying Clip-On Wheel Weight Types
NOTE: When balancing factory aluminum wheels with clip-on wheel
balance weights,
be sure to use special polyester-coated weights. These coated weights reduce
the potential for corrosion and damage to aluminum wheels.
These coated weights reduce the potential for corrosion and damage to
aluminum wheels.
- MC (1) and AW (2) series weights are approved for use on aluminum
wheels.
- P (3) series weights are approved for use on steel wheels only.
- T (4) series coated weights are approved for use on both steel and
aluminum wheels.
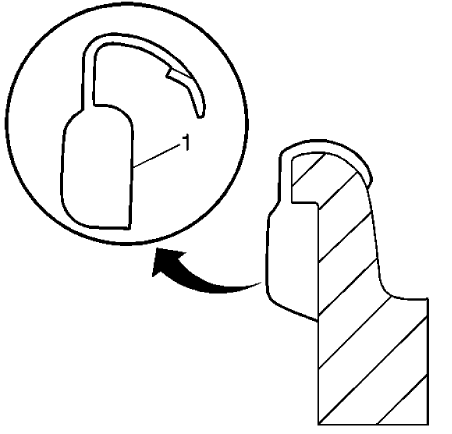
Fig. 21: Attaching Clip-On Wheel Weight
NOTE: Use a nylon or plastic-tipped hammer when installing coated
clip-on wheel
balance weights to minimize the possibility of damage to the polyester coating.
The contour and style of the wheel rim flange will determine which type of
clip-on wheel weight (1) should be
used. The weight should follow the contour of the rim flange. The weight clip
should firmly grip the rim flange.
Wheel Weight Placement - Clip-on Weights
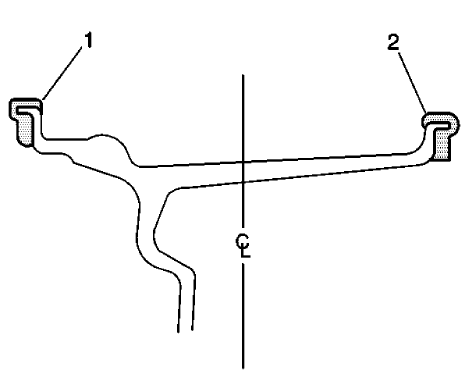
Fig. 22: View Of Wheel Weight Placement - Static Balancing
When static balancing, locate the wheel balance weights on the inboard flange
(2) if only 28 g (1 oz) or less is
called for. If more than 28 g (1 oz) is called for, split the weights as equally
as possible between the inboard (2)
and outboard (1) flanges.
When dynamic balancing, locate the wheel balance weights on the inboard (2) and
outboard (1) rim flanges at
the positions specified by the wheel balancer.
Adhesive Weights
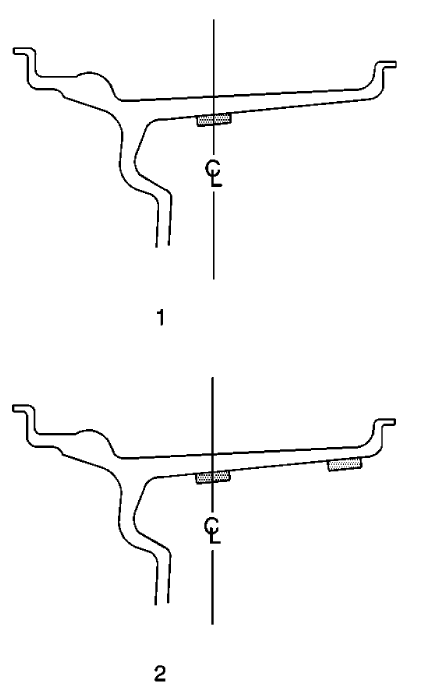
Fig. 23: Identifying Adhesive Weight Wheel Placement
NOTE: When installing adhesive balance weights on flangeless
wheels, do NOT install
the weight on the outboard surface of the rim.
Adhesive wheel balance weights may be used on factory aluminum wheels.
Perform the following procedure to
install adhesive wheel balance weights.
- Determine the correct areas for placement of the wheel weights on the
wheel.
- When static balancing, locate the wheel balance weights along the wheel
centerline (1) on the inner
wheel surface if only 28 g (1 oz) or less is called for. If more than 28 g
(1 oz) is called for, split the
weights as equally as possible between the wheel centerline and the inboard
edge of the inner wheel
surface (2).
- When dynamic balancing, locate the wheel balance weights along the wheel
centerline and the
inboard edge of the inner wheel surface (2) at the positions specified by
the wheel balancer.
- Ensure that there is sufficient clearance between the wheel weights and
brake system components.
NOTE: Do not use abrasives to clean any surface of the wheel.
- Using a clean cloth or paper towel with a general purpose cleaner,
thoroughly clean the designated
balance weight attachment areas of any corrosion, overspray, dirt or any
other foreign material.
- To ensure there is no remaining residue, wipe the balance weight
attachment areas again, using a clean
cloth or paper towel with a mixture of half isopropyl alcohol and half
water.
- Dry the attachment areas with hot air until the wheel surface is warm to
the touch.
- Warm the adhesive backing on the wheel balance weights to room
temperature.
- Remove the protective covering from the adhesive backing on the back of
the balance weights. DO NOT
touch the adhesive surface.
- Apply the wheel balance weights to the wheel, press into place with hand
pressure.
- Secure the wheel balance weights to the wheel with a 90 N (21 lb) force
applied with a roller.
TIRE AND WHEEL ASSEMBLY BALANCING - ON-VEHICLE
Special Tools
EL-38792-A Electronic Vibration Analyzer (EVA) 2
If after following the tire and wheel vibration diagnostic process, some
amount of tire and wheel vibration is
still evident, an on-vehicle high-speed spin balancer may be used to perform an
on-vehicle balance in an attempt
to finish balance the tire and wheel assemblies, wheel hubs, brake rotors, brake
drums, if equipped, and wheel
trim, if equipped, simultaneously. On-vehicle balancing can also compensate for
minor amounts of residual
runout encountered as a result of mounting the tire and wheel assembly on the
vehicle, as opposed to the
balance which was achieved on the off-vehicle balancer.
In order to perform an on-vehicle balancing procedure, carefully follow the
on-vehicle balancer manufacturer's
specific operating instructions and carefully consider the following information
before proceeding:
- Vehicles equipped with low profile, wide tread path, high performance
tires and wheels are susceptible to
small amounts of dynamic imbalance.
- When performing an on-vehicle balance, great care must be taken when
placing the wheel balance
weights on the wheels. If the wheel balance weights are not placed
accurately, they can actually induce
dynamic imbalance and thus increase the severity of the vibration.
- Inspect the vehicle wheel bearings to ensure that they are in good
condition.
- Thoroughly inspect all on-vehicle balancing equipment and ensure that it
is fully within the
manufacturer's recommended specifications.
- Do not remove the off-vehicle balance weights. The purpose of on-vehicle
balance is to fine tune the
assembly balance already achieved off-vehicle, not to start over.
- Leave all wheel trim installed whenever possible.
- If the on-vehicle balancer calls for more than 56 g (2 oz) of additional
weight, split the weight between
the inboard and outboard flanges of the wheel, so as not to upset the
dynamic balance of the assembly
achieved in the off-vehicle balance. For wheel balance weight information,
refer to Tire and Wheel
Assembly Balancing - Off Vehicle.
- If available, tape-off an area on top of the fenders and the quarter
panels, then place the vibration sensor
of the EL-38792-A Electronic Vibration Analyzer (EVA) 2 on the fender or
quarter panel above the
specific tire and wheel assembly while it is being on-vehicle balanced.
The EL-38792-A Electronic Vibration Analyzer (EVA) 2 will provide a visual
indication of the
amplitude of the vibration, and the effect that the on-vehicle balance has on
it.
TIRE-TO-WHEEL MATCH-MOUNTING (VECTORING)
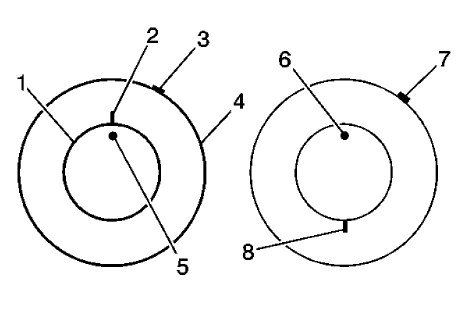
Fig. 24: View Of Tire-to-Wheel Match-Mounting
NOTE: After remounting a tire to a wheel or after replacing a tire
and/or a wheel,
remeasure the tire and wheel assembly runout in order to verify that the amount
of runout has been reduced and brought to within tolerances. Ensure that the
tire and wheel assembly is properly balanced before reinstalling to the vehicle.
- Mark the location of the high spot (3) on the tire as determined during
the off-vehicle tire and wheel
assembly runout measurement.
- Place a reference mark (2) on the tire sidewall at the location of the
valve stem (5).
- Always refer to the valve stem as the 12 o'clock position.
- Refer to the location of the high spot (3) by its clock position on the
wheel, relative to the valve
stem.
- Mount the tire and wheel assembly on a tire machine and break down the
bead. Do not dismount the tire
from the wheel at this time.
- Rotate the tire 180 degrees on the rim so that the valve stem reference
mark (8) is now at the 6 o'clock
position in relation to the valve stem (6). You may need to lubricate the
bead in order to easily rotate the
tire on the wheel.
- Reinflate the tire and seat the bead properly.
- Mount the assembly on the tire balancer and remeasure the runout. Mark
the new location of the assembly
runout high spot on the tire.
- If the assembly runout has been reduced and is within tolerance, no
further steps are necessary. Balance
the tire and wheel assembly, then install the assembly to the vehicle. Refer
to the following:
- Tire and Wheel Assembly Balancing - Off Vehicle
- Tire and Wheel Removal and Installation
- If the clock location of the high spot remained at or near the original
clock location of the high spot (7)
and the assembly runout has NOT been reduced, the wheel is the major
contributor to the assembly
runout concern.
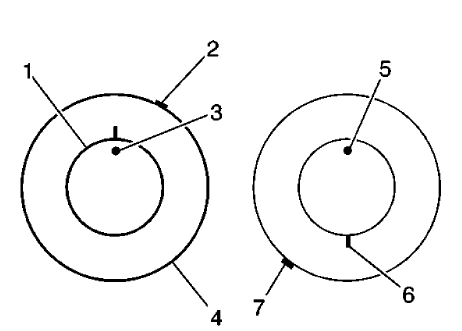
Fig. 25: View Of Match-Mounting Tire-To-Wheel
- If the clock location of the high spot has moved, however the assembly
runout has NOT been reduced,
perform the following steps:
- If the clock location of the high spot (7) is now at or near a position
180 degrees from the original
clock location of the high spot, the tire is the major contributor to the
assembly runout concern.
- If the clock location of the high spot is now in-between the 2 extremes,
then both the tire and the
wheel are both contributing to the assembly runout concern. Rotate the tire
an additional 90 degrees
in both the clockwise and the counterclockwise directions to obtain the
lowest amount of assembly
runout.
TIRE AND WHEEL ASSEMBLY-TO-HUB/AXLE FLANGE MATCH-MOUNTING
NOTE: After remounting a tire and wheel assembly to a hub/axle
flange, remeasure the
tire and wheel assembly on-vehicle runout in order to verify that the amount of
runout has been reduced and brought to within tolerances.
- Mark the location of the high spot on the tire and wheel assembly as
determined during the on-vehicle tire
and wheel assembly runout measurement.
- Place a reference mark on the wheel stud that is located closest to the
wheel valve stem.
- Always refer to the reference mark on the wheel stud as the 12 o'clock
position.
- Refer to the location of the high spot by its clock position on the tire
and wheel assembly, relative
to the marked wheel stud.
- Remove the tire and wheel assembly from the hub/axle flange. Refer to
Tire and Wheel Removal and
Installation .
- Rotate the tire and wheel assembly as close to 180 degrees as possible
on the hub/axle flange, so that the
wheel valve stem is now approximately at the 6 o'clock position in relation
to the marked wheel stud.
- Reinstall the wheel lug nuts to secure the tire and wheel assembly in
the new position. Refer to Tire and
Wheel Removal and Installation .
- Remeasure the tire and wheel assembly on-vehicle runout. Mark the new
location of the assembly onvehicle
runout high spot on the tire. Refer to Tire and Wheel Assembly Runout
Measurement - On-
Vehicle.
- If the assembly on-vehicle runout has been reduced and is within
tolerance, no further steps are necessary.
- If the assembly runout has NOT been reduced, perform the following
steps:
- If the clock location of the high spot remained at or near the original
clock location of the high spot,
the hub/axle flange and/or the brake rotor/drum mounting flange is the major
contributor to the
assembly on-vehicle runout concern.
- If the clock location of the high spot is now at or near a position 180
degrees from the original
clock location of the high spot, the tire and wheel assembly is the major
contributor to the assembly
on-vehicle runout concern.
- If the clock location of the high spot is now in-between the 2 extremes,
then both the tire and wheel
assembly and the hub/axle flange are contributing to the assembly on-vehicle
runout concern.
Rotate the tire and wheel assembly as close to an additional 90 degrees as
possible in both the
clockwise and the counterclockwise directions to obtain the lowest amount of
assembly on-vehicle
runout.
READ NEXT:
Vibration Theory
The designs and engineering requirements of vehicles have undergone drastic
changes over the last several
years.
Vehicles are stiffer and provide more isolation from road input than
Special Tools
EL-38792-25 Inductive Pickup Timing Light
EL-38792-A Electronic Vibration Analyzer 2 (EVA 2)
For equivalent regional tools, refer to Special Tools and Equipment.
The EL-38792-A Elect
SEE MORE:
Removal Procedure
WARNING: Do not attempt to repair or alter the head impact
energy-absorbing
material glued to the headliner or to the garnish trims. If the material
is damaged, replace the headliner and/or the garnish trim. Failure to
do so could result in personal injury.
CAUTION: If a vehicle i
Special Tools
J-2619-01 Slide Hammer
J-45019 Flange Remover
For equivalent regional tools, refer to Special Tools .
Removal Procedure
Raise and support the vehicle. Refer to Lifting and Jacking the Vehicle
.
Remove the wheel drive shaft. Refer to Rear Wheel Drive Shaft
Replacement .
Fi