Chevrolet Trax: Brake rotor assembled lateral runout correction
NOTE:
- Brake rotor thickness variation MUST be checked BEFORE checking for
assembled lateral runout (LRO). Thickness variation exceeding the
maximum acceptable level can cause brake pulsation. Refer to Brake
Rotor Thickness Variation Measurement.
- Brake rotor assembled lateral runout (LRO) exceeding the maximum
allowable specification can cause thickness variation to develop in the
brake rotor over time, usually between 4,800-11,300 km (3,000-7,000 mi).
Refer to Brake Rotor Assembled Lateral Runout Measurement.
Review the following acceptable methods for bringing the brake disc assembled
LRO to within specifications.
Determine which method to use for the vehicle being repaired.
- The indexing method of correcting assembled LRO is most effective when
the LRO specification is only
exceeded by a relatively small amount: 0.025-0.127 mm (0.001-0.005 in).
Indexing is used to achieve the
best possible match of high spots to low spots between related components.
Refer to Brake Rotor
Assembled Lateral Runout Correction - Indexing.
- The on-vehicle brake lathe method is used to bring the LRO to within
specifications through
compensating for LRO while refinishing the brake rotor. Refer to Brake Rotor
Assembled Lateral
Runout Correction - On Vehicle Lathe.
If the assembled LRO cannot be corrected using these methods, then other
components must be suspected as
causing and/or contributing to the LRO concern.
BRAKE ROTOR ASSEMBLED LATERAL RUNOUT CORRECTION - INDEXING
Special Tools
CH-45101-100 Conical Brake Rotor Washers
For equivalent regional tools, refer to Special Tools.
WARNING: Refer to Brake Dust Warning .
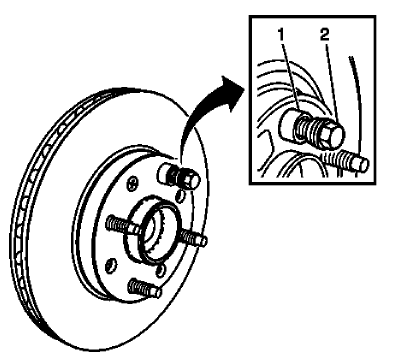
Fig. 80: One Lug Nut & Conical Brake Rotor Washers
NOTE:
- Remove the CH-45101-100 conical brake rotor washers and the lug nuts
that were installed during the
assembled LRO measurement procedure.
- Inspect the mating surface of the hub/axle flange and the brake rotor to
ensure that there are no foreign
particles or debris remaining.
- Index the brake rotor in a different orientation to the hub/axle flange.
- Hold the rotor firmly in place against the hub/axle flange and install
one of the CH-45101-100 conical
brake rotor washers (1) and one lug nut (2) onto the upper-most wheel stud.
- Continue to hold the rotor secure and tighten the lug nut firmly by hand.
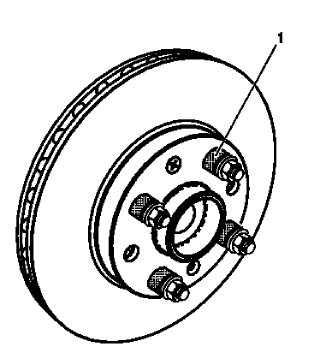
Fig. 81: Wheel Studs
- Install the remaining CH-45101-100 conical brake rotor washers and lug
nuts onto the wheel studs (1)
and tighten the nuts firmly by hand in the tightening sequence.
- Tighten the lug nuts in sequence, in order to properly secure the rotor.
Refer to Tire and Wheel Removal
and Installation .
- Measure the assembled LRO of the brake rotor. Refer to Brake Rotor
Assembled Lateral Runout
Measurement.
- Compare the amount of change between this measurement and the
original measurement.
- If this measurement is within specifications, proceed to step 14.
- If this measurement still exceeds specifications, repeat steps 1-9 until
the best assembled LRO
measurement is obtained.
- Matchmark the final location of the rotor to the wheel studs if the
orientation is different than it was
originally.
- If the brake rotor assembled LRO measurement still exceeds the maximum
allowable specification, refer
to Brake Rotor Assembled Lateral Runout Correction.
- If the brake rotor assembled LRO is within specification, install the
brake caliper and depress the brake
pedal several times to secure the rotor in place before removing the
CH-45101-100 conical brake rotor
washers and the lug nuts.
READ NEXT:
Special Tools
CH-45101-100 Conical Brake Rotor Washers
For equivalent regional tools, refer to Special Tools.
WARNING: Refer to Brake Dust Warning .
Fig. 80: One Lug Nut & Conical Brake Rotor Wa
DISC BRAKE SYSTEM DESCRIPTION AND OPERATION
System Component Description
The disc brake system consists of the following components
Disc Brake Pads
Applies mechanical output force from the hydraulic b
SEE MORE:
Torque Converter Stator
The torque converter stator roller clutch can have 2 different malfunctions.
The stator assembly freewheels in both directions.
The stator assembly remains locked up in both directions.
Poor Acceleration at Low Speed - Stator Roller Clutch Freewheels at All
Times
If the
Removal Procedure
Remove the battery tray. Refer to Battery Tray Replacement .
Remove the front bumper fascia opening upper cover. Refer to Front
Bumper Fascia Opening Upper
Cover Replacement .
Without draining the coolant or removing the hoses, remove and position
aside the radiator surge